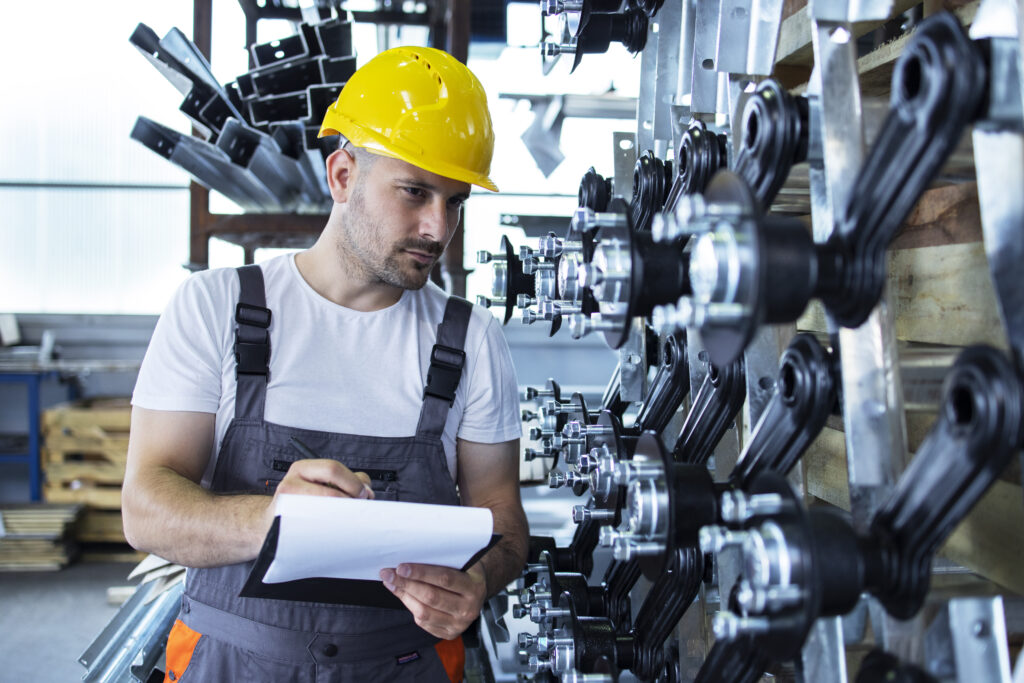
How to Build a Sustainable Spare Parts Inventory for Heavy Equipment
This paper aims at discussing how to achieve sustainable spare part inventory management for heavy equipments. Whether you are in construction business, mining industry, or use heavy equipment, having the right spare parts at the right time will help reduce on working time lost, increase on productivity and save on costs in the long run. One of the critical requirements in the management of spare parts is to have a well-ordered and sustainable stock that would not cause any halt in operations and would keep the machines in their optimal form.
In this part of the blog, we will help you understand the main steps to undertake in order to effectively create and manage spare parts inventory of heavy equipment.
1. Identify Critical Spare Parts
The first thing in the construction of sustainable inventory is to establish the essential spare parts for the machinery. These are those components that are most vital in performing the equipment’s central functions for instance engine components, hydraulic systems, filters, electrical systems, and fan belts. Divide parts into high and low importance, depending on how often they are used, so you can store the most vital ones.
So, examine the historical breakdown data of your equipment to determine which components fail most frequently and are likely to be required. This process will also assist you in not buying more parts than required, which may lead to wastage of inventory and additional space for storage.
2. Set Inventory Thresholds
The process of establishing the inventory thresholds, also known as reorder points for every spare part, makes it possible to set the right stocks levels. This system will help to place an order when the quantity of a certain part is low to avoid cases where there is no part in stock. Specific numbers for inventory should be established depending on the part’s importance, time for procurement, and usage frequency.
This should be done with the help of the inventory management software that is able to indicate the current state of stocks and when it is high time for purchasing products. This will assist in ensuring that there are few interferences or hitches in the supply chain.
3. Implement an Effective Inventory Management System
The elements include an efficient inventory management system (IMS) which is responsible for the tracking of spare parts stock, location and status. A digital IMS enables you to have an account of the supplies and their use, as well as the time or level at which you should order a new batch. Furthermore, it makes it easier for you to predict more future part requirements given that you monitor equipment maintenance trends.
Ensure that the system fits your procurement procedure so that it can automatically order from the suppliers at certain predefined levels. This integration will not only reduce time but also has the advantage of reducing human errors as much as possible.
4. Source Reliable Suppliers
The key to a sustainable inventory is based entirely on the supplier base, which has to be credible. Dealing with reputable suppliers assure you of quality spare parts hence you avoid machinery breakdowns due to lack of spares. Focus on those suppliers who can offer a large number of part numbers, short lead times, and quality services.
For heavy equipment spare parts, you can rely on Al Saif Al Malaki – heavy equipment spare parts supplier. They particularly focus at offering quality spare parts so that your machines can continue to operate.
5. Optimize Storage and Handling
There are some important factors that should be followed in order to preserve the quality of spare parts and some of them are: Some of them like engine parts and electrical parts need to be protected so that they do not get damaged over time. Make certain that your warehouse area or storage center is well-organized, and safely and properly lit with the correct temperature to avoid spoilage. Use labels and put the parts in categories that can be easily identified or in areas that are designated based on the criticality of the part or how often they are used to minimize time lost searching for the parts.
6. Regularly Review and Audit Inventory
Spare parts should be audited and reviewed periodically to make sure that they are still manageable and sustainable. Identify which of the part is in excess, which one is scarce, and which of them need not be ordered again because they are no longer in use. This review process helps one avoid having capital locked up in raw materials only to find they are not used, while at the same time not being caught unprepared when the vital items are out of stock.
Key factors that have been established in the management of spare parts inventory include the following; The key areas include identification of critical parts, setting up inventory control points, enforcement of inventory control mechanisms and dealing with reputable suppliers . This way, you can always be ready to fix both normal wear and tear as well as sudden failures that will help keep your business running.